Online shopping breathes life into 600 year old printing techniques
– BY ALLISON FRANKLIN, DEC. 19TH 2015
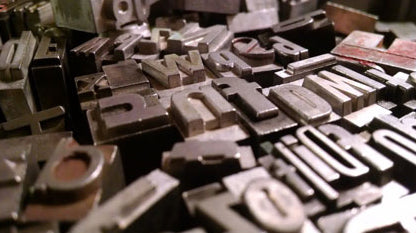
IF YOU PRINT IT, THEY WILL READ
In the 14th-century, Johannes Gutenberg spent almost two decades innovating the existing method printing.
Until then, entire pages were carved into a wooden block.
This method was tedious and time-consuming.
But, tedious as it was, this method was far faster than transcribing by hand.
Gutenberg’s new method allowed entire pages to be reproduced at once.
Then, the movable type could be reorganized for the next page to print.
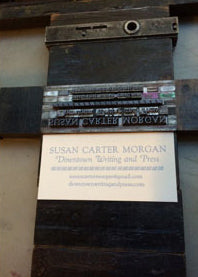
Downtown Writing and Press
These letters were then reassembled and organized to create the next page.
His letter tiles were carved onto the surfaces of wooden blocks which wore down over a short time.
Soon, these wooden versions were replaced by more durable metal type.
His process introduced printed books to the common people for the first time.
The letterpress was increasing the availability of news, current events, history and philosophies.
His method became the standard for printing for the next 300 years.
Guttenberg’s handpress allowed for a clean, even distribution of ink across each page.
His blended ink was being pressed onto an average of six pages per day.
The industrial revolution was strongest in American manufacturing and production.
The printing process was no exception.
COLOR ME PINK AND PURPLE, PLEASE MR. LITHOGRAPH
In 1798, Alois Senefelder invented the process which came to be known as lithography.
Lithography was desirable by many for its clean, even reproduction.
It allowed the entire printed area to remain on a level surface by casting entire lines of text from metal.
These lithographic presses were being powered by steam engines.
They were much faster than the original letterpress.
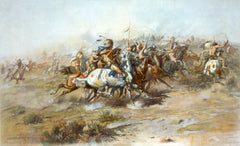
by - Charles Marion Russell
They also introduced the application of more than one color to individual pages.
Old model presses were altered so that consistent pressure was possible with each run.
Before then, full-sized presses had to be worked by foot while paper was fed into the press by hand.
These were updated to newer versions with motors that fed paper into the machine.
The presses could print thousands of copies per hour while being monitored for quality.
THE DIGITAL ERA WREAKS HAVOC ON THE LETTERPRESS
FEELING A BIT SET OFF, LET’S BURN SOME RUBBER!
In 1903, an American printer modified his press to print from rubber rollers rather than from stone.
Ira Washington Rubel had thus created offset printing.
This was the height of mass production for printers.
Then, daily newspapers were faster and more affordable to print.
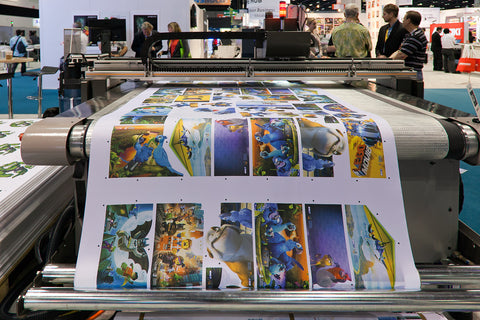
This method dominated the lithographic technique through the the end of the second world war.
With the rise of the digital era, we begin to see the rapid decline of letterpress printing.
As computers became more common, individuals could print through digital or offset methods.
Consumers now had the power to print from their own homes.
This ease of individual production caused many studios and shops to struggle.
Medium sized shops began to liquidate their inventory of presses to larger scale operations.
To decrease production costs, many manufacturers began replacing workers with machines.
There was a concentrated effort among producers to increase efficiency.
This meant that many of the roles filled by people were becoming automated.
After World War II, printing had made a noticeable leap.
This meant that the old machines were now taking up space.
Lithography had given way to offset printing and hand-set type was a dying process.
People were only required to watch these machines to ensure quality.
Then, beginning in the 1980’s, the rise of personal computing led to a rise in desktop publishing.
Ink jet printers were cheap and easy to operate.
Many companies were born and grew out of this period.
Most were joining the race to innovate automation.
Automation also meant cleaner and more consistent finished products.
It became less desirable to see the marks of handmade.
Fewer printers were working in a tactile, hands-on process.
The definition of quality was cleaner, smoother for most consumers.
The ‘kiss’ became the new standard for printers.
A ‘kiss’ refers to the press only touching the paper enough to transfer the ink.
‘Kissing’ the paper was superior to the technique that resulted in depressions.
This was considered preferable according to most of the consumers of the day.
IN THE WORLD OF COMPUTERS, THERE IS A BLISSFUL RESURGENCE OF HANDMADE ART.
For the past decade, there has been a resurgence of traditional techniques in many art forms.
Many of these converting artists want more of a hands-on relationship with their art.
The tactile process offers more than computer art and design might have to offer.
There are thousands of artists and studios offering their handmade products and custom services.
Many of these artists are marketing their creations through the online marketplace, Etsy.
These stores range in scale from individuals and families to large scale operations.
The iron presses that have been idle for decades have been restored and put back to work.
Times, and tastes, have changed though.
Now, the inconsistencies of handmade are preferable.
Unfortunately, graphic designers today rarely have any hands on experience with setting type.
Most designers today work from computer workstations.
Computers allow individuals to manage large scale projects alone.
But, many creative professionals have begun to explore traditional techniques.
They are stepping away from the isolation of computer dominated methods.
And, consumers are stepping up in support of these explorations.
Finding an artist or studio that appeals to an individual’s taste is no longer difficult.
Consumers worldwide now have access to great marketplaces for custom printing.
Creating an online Etsy store is easy.
Now, small studios can compete with larger production houses.
Mass-produced greeting cards are losing popularity.
Consumers are choosing products with their own signature styles.
And, what people once thought of as defects are now becoming desirable.
REVOLUTIONARY MARKETPLACE OPENS NEW OPPORTUNITIES FOR PRINTERS.
Artists from several different backgrounds make up today’s marketplace.
For some, the skills and experience came from working in print shops.
Others set out to teach themselves through trial and error or online resources.
Many schools and universities also offer letterpress training as an alternative to commercial design.
There are classes in traditional printing technique through community colleges and through graduate universities.
Getting a press can be the most challenging phase for any up and coming studios.
As the community of letterpress artists evolves, presses change hands and continue producing.
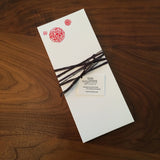
Museums sell presses from their collections.
Collectors begin using their accumulated presses and type.
Through either of these routes, equipment transitions from being display pieces to active production.
The popularity of hand printed cards has opened doors for many printers to explore their art.
Most of the studios on Etsy sell more greeting cards than anything else.
But the range of these cards is vast.
The most popular cards tend to be custom variations of a studios style.
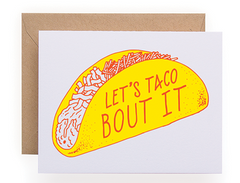
Or playful themes that are blank inside.
The artistic freedom goes well beyond this though.
Many studios are printing limited edition series of fine art.
They are utilizing the letterpress as a medium in their multimedia work.
The multimedia aspect extends to their products as well.
Greeting cards with pressed type adorned by water color or ink drawings.
Some press work acting as a foundation for paint or collage.
A computer workstation is not taboo in an artists studio that prides itself in handmade work.
Through the use of polymer plates, many printers are more versatile.
Designs created on a computer can used to create plates from which presses create the final piece.
But, there is a distinct trend that goes the other direction.
Many printers are converting from a digital workflow to a hands-on process.
Besides the use of polymer plates, artists are moving to the tactile process.
After becoming disenchanted with the digital workflow, the tangible process becomes almost therapeutic.
Whether digital, analog or hybrid, artists are investing themselves into printing.
The printing process has become almost as popular as the printed products.
Most of the studios we’ve interviewed for this article are growing and plan on continuing to grow.
Don’t be surprised to see an increasing number of hand printed art when you open your mailbox.
*A Special Thank You
An added bonus as a gesture of our gratitude for these and all printers helping to keep handmade art alive, we would like to offer you a sample of INK SOLV 30 industrial hand cleaner.
We would like to thank the following printers and studios for their time and invaluable input for this article.
Please visit their stores on Etsy and help support handmade art!
- Blake Martin at Sparkvites
- Susan Carter Morgan at Downtown Writing and Press
- Shayna at Steel Petal Press
- Melissa Baldwin at Elf Letter Press
- Jennifer Ferrell at Starshaped Press
- Macarena Gonzales Hopff at Milletter Press
- Keetgi Kogan at Monkey Business Press
- Teresa Tonai at Little Trees Studio
Works cited:
About INK SOLV 30
There are many hand cleaners out there, some work better than others.
Here at INK SOLV 30, we like to think that because we were originally developed in 1937 to remove ink stains specifically for workers in the printing industry, we are the best of the best.
We'll send you a free sample to prove it to you!
We are tired of being the industry's best kept secret. It is time to let this little hand cleaner out of the proverbial bag!
INK SOLV 30 would like to send you a free sample of our super strength industrial hand cleaning powder specifically formulated to remove the most stubborn dyes and printing inks.
INK SOLV 30 has an extremely long shelf-life; unlike goops and lotions that will degrade and separate over time, INK SOLV 30 maintains its cleaning power for years. You will NOT be disappointed!
Even if you think your current hand cleaner works moderately well, we'd like you to accept our challenge! With just a teaspoon of our product, mixed with enough water from your faucet to form a paste, there isn't another cleaner around that can remove ink from hands as well as INK SOLV 30!
In closing, as Tony Jimenez (an Ink Room Manager) put it so simply, “Knowledge about the industry… Is a must”! We believe that extends to knowing about the cleaners you use too! Go on, give us a try!
Because you shouldn't have to wear your work home!
Leave us a comment, we'd really like to hear your input!
*Data for this article was collected from letterpress shop owners found on the Etsy.com online market through an online survey developed and produced by INK SOLV 30, the printing industry’s hand cleaner of choice since 1937.